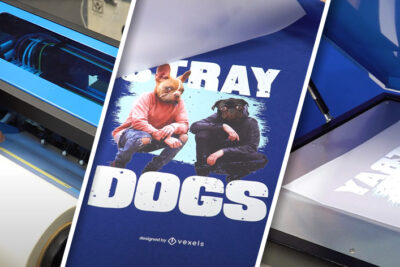
😱 DTF problems and their solutions
😱 DTF problems and their solutions
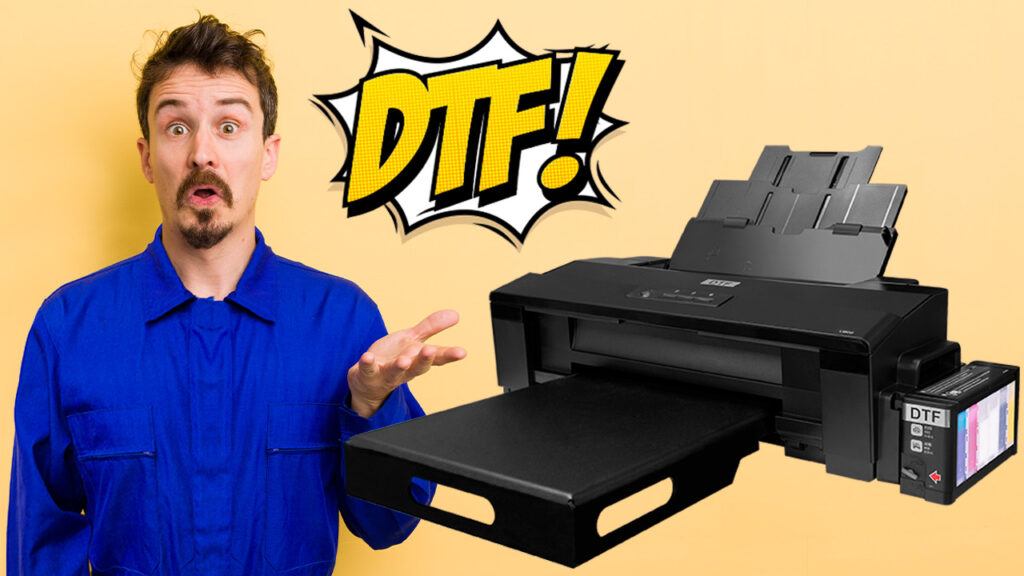
The technique DTF technique is increasingly used by our clients. And rightly so. They know that with a low investment they can start stamping on different surfaces. In both cotton and polyester fabrics. Also in wooden products, mugs or objects such as skateboards...
If you have already switched to DTF or you are interested, we want to help you. We have compiled the main DTF problems to give you solutions. With these tips, you will be an expert and will have your printer in perfect condition. Interested? Let's get started!
DTF printer parts
Before knowing the most common DTF problems, it is necessary to know the parts of the printer.
- Ecotank. Container where the ink tanks are located. You must make sure that the ink occupies at least one third of its capacity.
- Residual ink reservoir. To prevent the pad from filling up, a waste ink reservoir, i.e. the liquid from head cleaning and maintenance, is added. It is necessary to empty this container to prevent breakdowns.
- Dampers. Refers to the cartridges on the head. These are attached to the Ecotank with a tube.
- Header. Part that takes care of the printing, so it needs special care. Later we will explain its maintenance and how to change it if necessary.
- Capping. Where the printhead rests and the waste ink is discharged. This accessory keeps the head in good condition.
- Wiper. Rubber tab that cleans the head when it comes out of the capping.
You know the parts. Now, let's solve the DTF problems!
No color is displayed
If this is the first time you turn on the printer, you may have this problem. We explain how to solve it:
- INITIAL INK LOADING: The first step is to load the inks into your DTF printer. DTF printer. To do this, open the cap of one of the tanks and fill it with its corresponding ink. You must load it with the correct color, usually marked with stickers. Keep all caps closed except the one you are filling or you may contaminate some ink. When the tanks are full, turn on the printer and press the drop icon for a few seconds. Initial loading will begin. It can last about 20 minutes.
It may happen that the initial charge is not completed correctly and no color appears during printing. To fix it, open the Resetter software provided with your printer purchase. Click on 'Particular adjustment mode', go to the 'Ink charge' option and click 'OK'. In the drop-down menu choose 'Initial ink charge', check 'Not increment waste ink pad counter' and click 'Ink charge'. It will ask you to restart the printer and it will perform the upload.
- ECOTANK LOCKOUT: Most often you have activated the lockout that cuts off the ink supply from the Ecotank to the printhead. This causes it to run out of ink when it runs out in the dampers. Make sure that this lock is deactivated before printing.
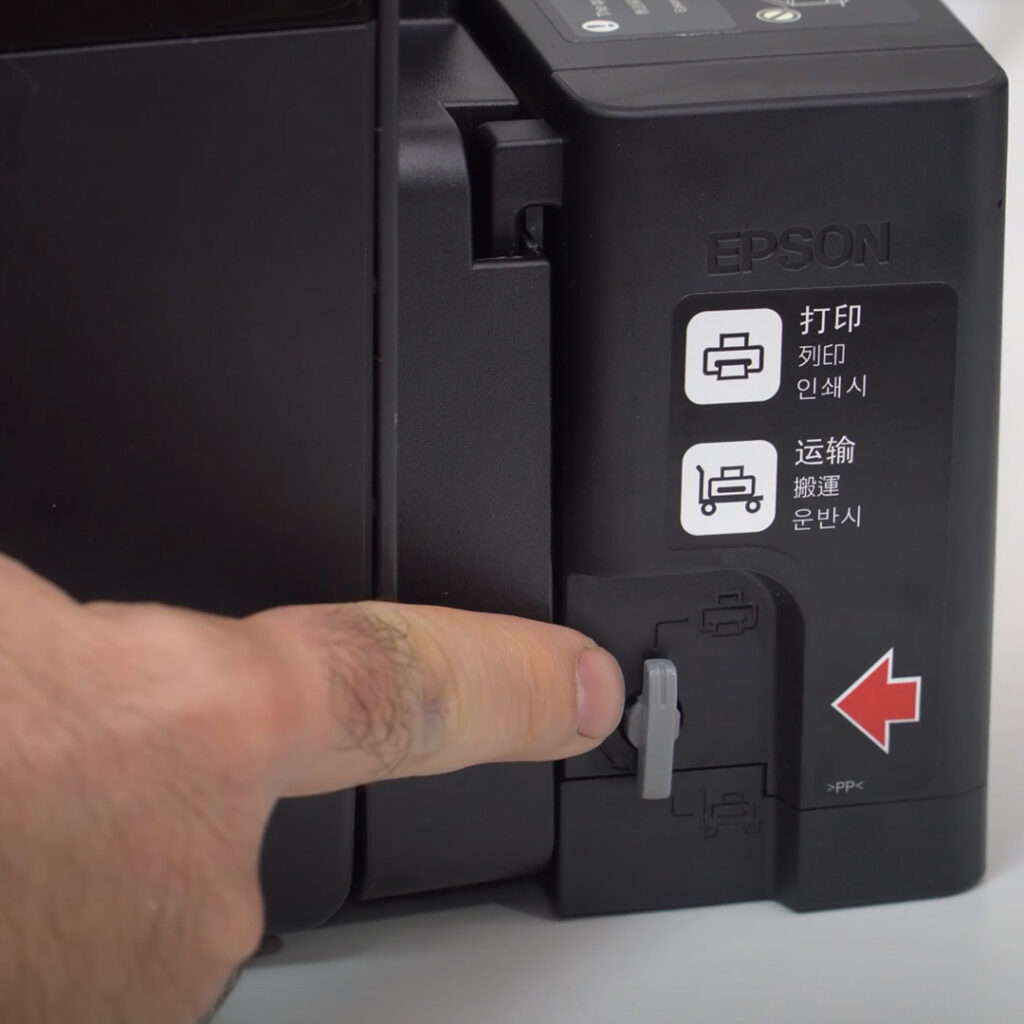
Does not print white ink or any of the colors
This is the most common problem. Most of the time this happens because of the white ink sediment, the main cause of all evils. The solutions to this problem are these:
- TANK SHAKING: Before performing any type of action, both printing and maintenance, you must shake the tanks to avoid sedimentation. It is a simple but effective action. You will avoid quite a few problems. Some current printers already have it as standard.
- HEAD CLEANING: Before starting to print, perform a simple head cleaning. If you usually have the printer active, this will be enough. Just go to 'Printing Preferences', 'Utilities' and 'Printhead Cleaning'. Perform a nozzle test to check if all colors are coming out correctly.
- BLAST CLEANING: If after a normal head cleaning, no white or color appears, you should do a blast cleaning. This cleaning will completely empty the circuit and the dampers. It will then refill it, generating pressure and unclogging the injectors.
- DAMPERS SHAKING OR REPLACEMENT: Every 15 days, it is recommended to shake the dampers. Turn on the printer and when the printhead unlocks, turn off the power. Tip! Use a power strip so as not to damage the connection by pulling. Place the head in the working position. Remove the screw from the cover and with the help of a flat screwdriver, loosen each dumper. Now shake them to avoid sediments. Check that there is no air inside. If they have air in them, you can absorb it using a syringe. If the dampers have a lot of sediment you may need to change them. You only have to loosen the tube and put in the new one. Reassemble everything and you're done.
- FLUSHING: Flushing consists of passing the cleaning liquid through the nozzles of the head . We will differentiate two types of Flushing, one without removing the head and the other by disassembling it completely. Let's look at the differences:
Flushing without removing the head
- Turn on the printer and when the printhead moves, turn off the power using a power strip. Remove the screw and printhead cover from the printhead.
- Place absorbent paper and move the head on top. Remove the cartridges with the help of a flat screwdriver, keeping them in order.
- Now pour some liquid into the container and fill the syringe a little.
- Insert the tube into the injector and, without excessive pressure, start injecting the liquid.
- Repeat the operation on the clogged injectors.
- Then put everything back in place.
Flushing by disassembling the head
- Turn on the machine and turn it off from the power strip when the head moves, in order to release it.
- Take it to the work area and remove the cover.
- Remove the dampers. Now you must release the right cover that holds the head flex cables with the help of a screwdriver.
- The next step is to remove the rear piece. Use a screwdriver to loosen the tabs located on each side. To release the head, remove the three screws using a magnetized screwdriver.
- Remove the head and place it upside down taking special care not to touch the silver part at any time or you will damage the head. Carefully release the flex cables at the same time.
- Use a swab to clean along the edge of the head that may have dried ink on the edge.
- Now use the syringe with the cleaning fluid to push it through each of the nozzles. Place a bucket or container underneath so as not to make a mess. You must apply pressure, but not too much. You will see the ink come out and then the cleaning fluid.
- When you are finished you must reassemble the head. You must place the cables correctly. Put the screws, protectors and finally put the dampers in place.
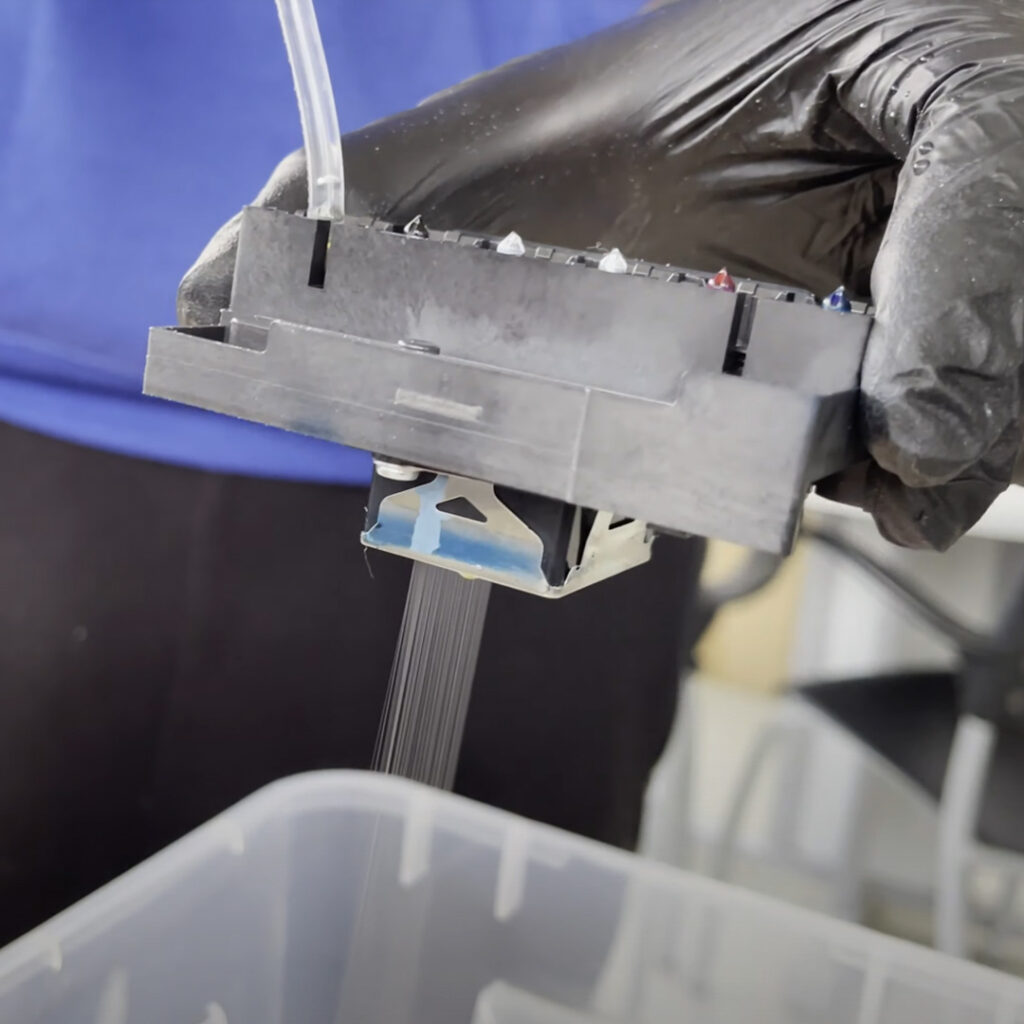
If, after exhausting the previous ways, ink still does not come out of any of the channels, you should probably replace the printhead. You have already read just above how to disassemble it. It is not complicated. Mount the new one and you will have the perfect printer again. We recommend that, when replacing the head, you also change the dampers.
Stains on paper or smudged design
Friction may occur during printing. As a result, the design is smeared because the ink is wet. It can also happen that the ink does not adhere to the film, leaving a kind of paste of mixed inks. Let's see how to solve it:
- PRINT ON THE RIGHT SIDE OF THE FILM: The film has a more porous side, which allows the ink to remain stable. Usually it is the matte part, but sometimes it is difficult to know which part of the film is printable . If you have made a mistake, you will see that the ink is mixed. It is because you are printing with too much ink or on the wrong side. But don't worry. Wipe the film with a cloth or paper, turn it over and print. You do not have to discard the film.
- TRAY PLACEMENT: Improper placement of the front tray can also cause this problem. If there is a sag or the front of the film is tripped, it will lift and the head will rub against the design. Make sure the tray is in contact with the printer, but does not obstruct the output.
- DRY INK ON THE HEAD OR WIPER: DTF ink is a gummy ink that deposits and solidifies. To keep the head clean, the wiper goes up and the head passes through the rubber removing any debris. The problem is that both the wiper, the capping and the head itself end up having gummy residues on the edges and must be removed . To do this, you must perform the operation of unlocking the head as in other maintenance. With the help of a screwdriver lift the wiper lever. You will see that it is full of dried ink. Clean it using tweezers and a swab dipped in cleaning fluid. Do it also on the capping, you will see that there is solid ink on the edge. As for the head, we have explained above how to clean the edges of the head when it is disassembled.
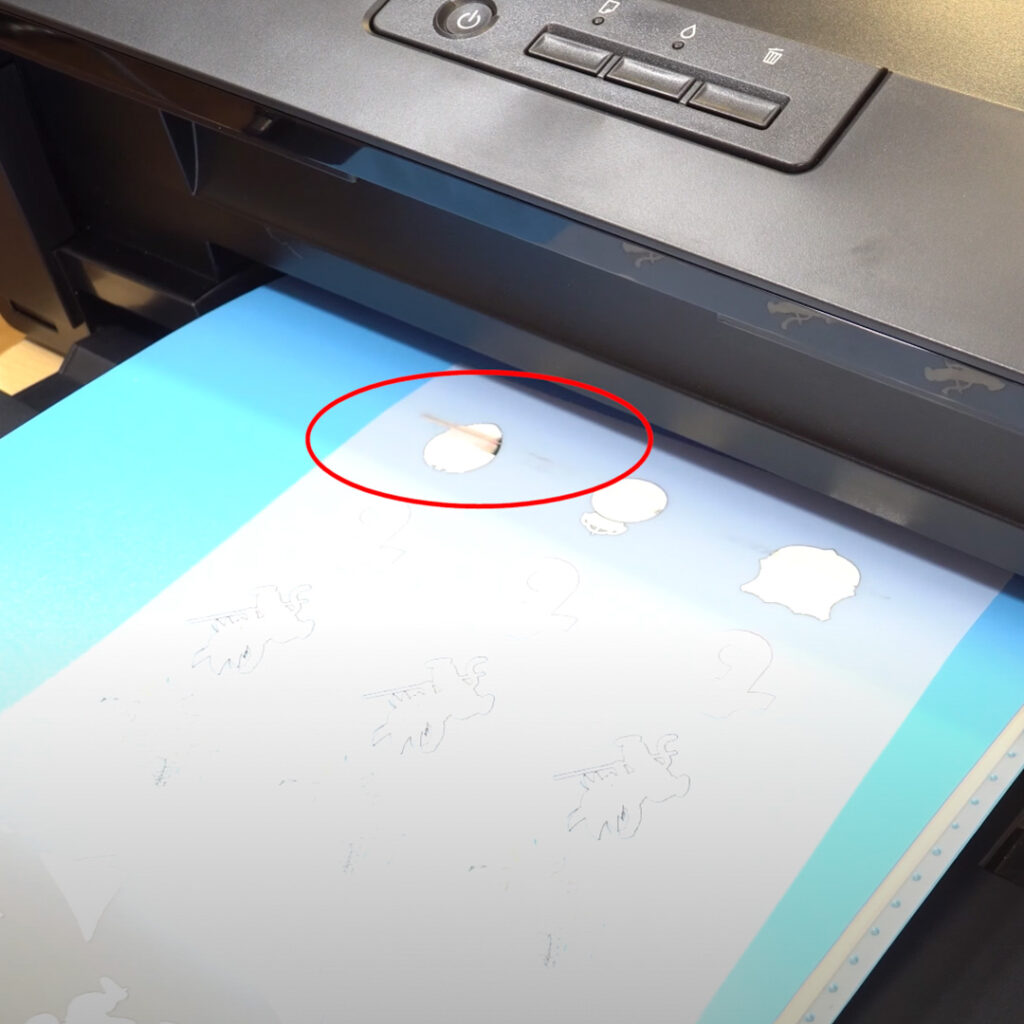
Problems with film loading
One of the most recurring DTF problems is a failure to load the film. Either because the printer fails to pick it up or because it passes it by. One of the most effective solutions is to place a board or a few sheets of foil in the tray to stiffen the film. This will ensure that the printer loads it correctly.
Another problem is dirt on the paper loading rollers, located on the right side, facing the front of the printer. To clean them use kitchen paper impregnated with alcohol. Bring it in contact with the roller and press the 'Feed Paper' button. Now clean the lower roller by rolling it.
Finally, if nothing has worked for you, the last trick is to put some painter's tape on the back of the bottom corner of the film. It will prevent it from slipping when loaded.
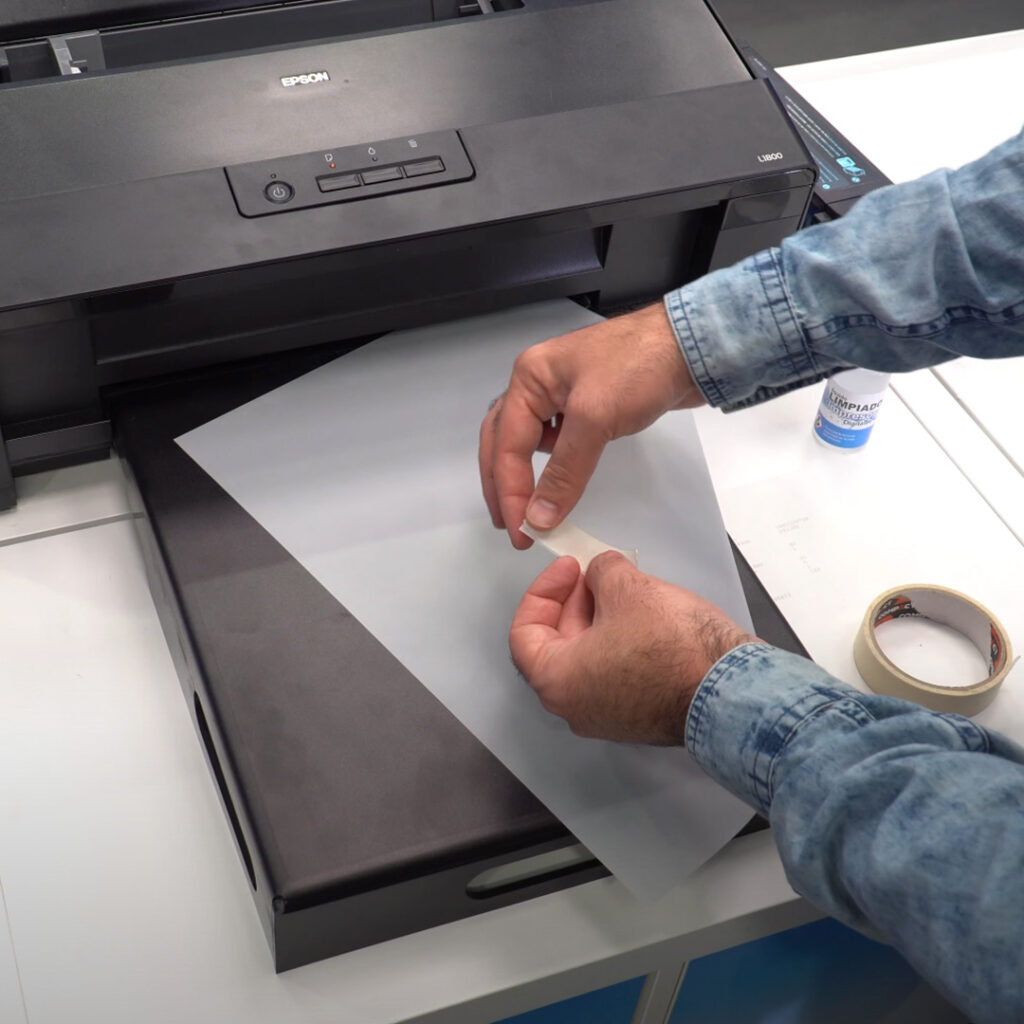
Lights on the DTF printer panel
On the front panel of the printer you may encounter two types of errors, in addition to those related to the paper.
- PAPER AND INK LIGHTS BLINKING ALTERNATIVELY: This is because the printer understands that the maintenance pad, which fills with waste ink, has reached the end of its useful life. As you know, the printer comes modified so that that ink goes into a waste ink tank and not into the pad, but the printer doesn't know that. To solve the error you must open the Resetter software that we have sent you with the antivirus deactivated. Enter 'Particular adjustment mode', choose 'Waste ink pad counter', press 'OK'. Press 'Check' to read the counters. Now click on the two holes and click 'Initialize'. It will ask you to turn the printer off and then turn it on. Now if you press 'Check' you will see the counters reset to zero and you will no longer get the error.
- PAPER AND INK LIGHTS FLASHING AT THE SAME TIME: This error is an indicator that something is wrong. There is a possible solution. Clean the encoder tape with an eyeglass wipe or a little alcohol. This is located on the metal guide.
This error can also happen when you move the head carriage without having unlocked and removed the power. In this case, with the printer turned off, return the carriage to the origin and start it even though you may have damaged it.
Software Problems
Some of the problems we encounter do not stem from the DTF printer or its maintenance, but from an incorrect configuration of the Digital Factory.
There are several points to consider.
- SOFTWARE AND DRIVERS UPDATE: The guys at CADlink are updating them to fix bugs and add functionality. We recommend that you have both the software and drivers updated. For the software go to 'Help', 'Check for updates' and follow the on-screen steps to update. For drivers go to 'Devices', 'Manage devices', choose your device and click on the world icon. If there are updates it will ask you if you want to install them, follow the steps on the screen and you are ready to go.
- DOES NOT PRINT TOO MUCH WHITE: In the software you have different print modes that you can modify and even create new ones. Basically, in the color settings, you can increase the percentage of white ink and the amount of white that will print underneath the black color. We have done a test using two different color modes. One at 80% ink density and 40% below black. The second, with 100% density and 100% below black. The differences can be seen at a glance.
- FAILURE TO PRINT BECAUSE OF PORT FAILURE: Sometimes, after printing has been launched, a failure in the port configuration may appear. If this happens, right-click on the file to be printed and click 'Remove error'. Now go to 'Jobs', 'Manage Queues', and in your printer click on the drop down and choose the correct port. Close and you are ready to print.
Here is a visual explanation of how to solve each of these DTF problems:
Conclusions of the DTF problems
-Ecotank: Container where the ink tanks are located.
-Residual ink reservoir. Liquid reservoir from head cleaning and maintenance.
-Dampers. Cartridges that are located on the head.
-Header. Part that is in charge of printing.
-Capping. Where the waste ink is discharged.
-Wiper. Rubber tab that cleans the head when it comes out of the capping.
The safety caps on the tanks may be closed. Also that you have activated the lockout that cuts off the ink supply. Another problem is that the initial charge has not been completed correctly. To solve it, open the Resetter software. Click on 'Particular adjustment mode', go to the 'Ink charge' option and click 'OK'.
Most of the time, it is caused by the sediment of the white ink or one of the colors.
We give you some solutions. You can agitate the tank to prevent sedimentation, clean or replace the heads, perform a jet cleaning, agitate or replace the dampers or clean the injectors.
This problem arises during printing, when there is friction. As a result, the design is smeared because the ink is wet. It can also happen that the ink does not adhere to the film.
It may be because the printer fails to pick it up or because it passes it by. One of the most effective solutions is to place a board or a few sheets of foil in the tray to stiffen the film. This will ensure that the printer loads it correctly.
One reason is that the printer detects that the maintenance pad has reached the end of its useful life. It can be corrected from the software. As you know, the printer comes modified so that that ink goes into a waste ink reservoir and not the pad. In case the lights flash at the same time, clean the encoder tape with alcohol.
With this DTF maintenance and troubleshooting manual, we hope we have helped you to solve the main difficulties of this technique. If you have any questions or if we have left anything out, please leave us a comment so that we can help you and other users can see it.
If you have any questions or if we have left anything out, leave us a comment so we can help you. You can also contact our Customer Service department.
Remember to check our social media, where we post plenty of ideas, offers and news from all areas of personalisation. Follow us on Instagram and Facebook to make sure you don't miss anything. Don't forget to subscribe to this Blog and to our Youtube channel.
If you liked it, don't leave without leaving your five stars!
See you soon in a new post!
WE WANT TO KNOW WHAT YOU THINK
You may also like