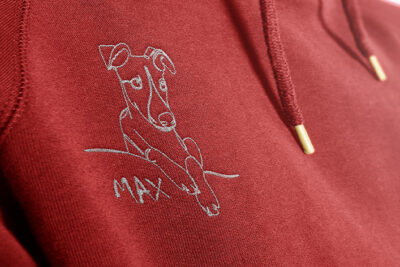
🪡 Embroidery Dictionary: Learn the Language of This Technique
🪡 Embroidery Dictionary: Learn the Language of This Technique
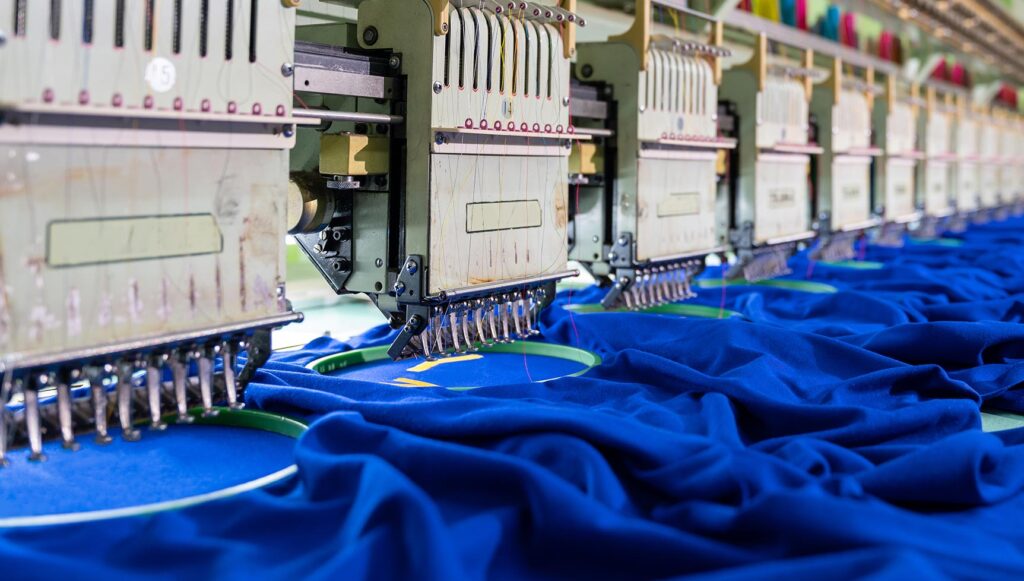
The world of embroidery has its own language, and we understand how challenging it can be to grasp, especially when common dictionaries do not include such specific terms.
We have created this glossary to help you master the key vocabulary of embroidery, covering everything from technical terms to those related to technology. Discover how to speak "embroidery language" like an expert!
A
Finishing Touch: The final step after completing the embroidery. It involves trimming loose threads, removing or trimming the stabiliser, cleaning any stains, ironing to remove wrinkles and hoop marks, and preparing the garment, either by folding or packaging it for presentation.
Stitch Shortening: A digitising technique that reduces the stitch length in curves or tight corners. This prevents excessive build-up that could cause thread breakage or damage to the fabric.
Ad Copy: Embroidered text on an item, which may include the name of an advertiser, a slogan, or a trademark.
Needle: A thin, sharp piece of steel with an eye for guiding the thread through the fabric. In machine needles, the eye is located at the tip, whereas in hand sewing needles, it is at the base. Its function is to enable the thread to pass through the material precisely.
Hook Timing Adjustment: The process of synchronising the hook with the needle movement, essential for forming precise stitches and ensuring high-quality embroidery.
Appliqué: An embroidery technique that uses pieces of fabric sewn during the process to add texture and colour to the design. It allows for the incorporation of eye-catching details without increasing the stitch count, replacing fill stitches, which are typically very dense.
- Reverse Appliqué: An embroidery technique that involves sewing a fabric onto the back of a garment. The garment is then cut from the front to reveal the underlying fabric, creating a unique decorative contrast.
GIF File: A widely used graphic file format for images. Its name stands for "Graphics Interchange Format" and it is known for supporting animations and having a small file size, making it ideal for web content.
B
Frame Support Bars: Components of the pantograph that hold and stabilise the frames during embroidery. They ensure precise movements, contributing to uniform and high-quality results.
Frame Placement Base: A device designed to facilitate the mounting of frames on fabrics or garments, ensuring precise centring and uniform tension. It is particularly useful in mass production, where repeatability and consistency are essential.
Tacking Stitches: Long stitches that connect different motifs within a design. These stitches, which are not part of the final embroidery, are manually removed with scissors or by automatic systems that perform the cutting during the embroidery process on modern machines.
Embroidery Hoop: A device made of wood, plastic, or metal that secures and stretches the fabric along with the stabiliser to ensure stability during embroidery. This allows the needle to work with precision and uniformity.
- Cap Frame: A specialised frame for embroidering pre-made caps. There are two main types: one that flattens the cap for flat embroidery and another that follows the natural curvature of the cap on tubular machines.
- Free-Motion Embroidery Hoop: An embroidery technique where the user manually guides the hoop, allowing for the creation of unique and personalised designs. Utilise zigzag stitches available on many machines to add creative details.
Blatt Stitch: A term derived from Schiffli (or shuttle) embroidery meaning "feeding thread". It describes long and closely placed zigzag stitches. In modern embroidery, this technique is known as Satin Stitch.
Knot Ball: Accumulation of thread underneath the garment, caused by incorrect thread tension, faulty threading, or poorly tensioned fabric. This issue can obstruct fabric movement and cause damage if not corrected.
Embroidery: A decorative technique for creating designs or text on fabric through stitching. Originally done by hand, it is now primarily carried out with computerised machines, ensuring precision and efficiency.
- Bobbin Work Embroidery: A method that uses the bobbin thread as if it were the top thread, placing the garment upside down in the hoop. It is ideal for simple designs and for working with special threads that cannot be threaded in the traditional way.
- Flat Embroidery: A process where the fabric is placed in flat hoops, positioned above the hook. It is suitable for embroidering non-tubular surfaces such as t-shirts, tablecloths, or fabric panels.
- Puffy or 3D Embroidery: A technique that uses foam as a base for embroidery, creating a three-dimensional raised effect with dense stitches. It is ideal for designs that require a striking visual impact.
- Tubular Embroidery: A method used in machines designed for embroidering garments or fabrics with a tubular shape, such as t-shirts or sweatshirts. The garments are placed around the hook to facilitate embroidery and achieve uniform finishes.
Buckram: A fabric reinforced with adhesive to stabilise materials during embroidery, serving as a substitute for interfacing. It is commonly used on the front panel of caps to provide firmness and ease the process.
Loops: Stitches that remain loose due to improper upper thread tension or machine setting issues. This defect can affect the embroidery quality if not corrected.
C
Bobbin: A spool of thread housed in the hook, which, together with the upper needle thread, forms the stitches. It is a system similar to that of sewing machines.
Bobbincase: A round metal piece where the bobbin is placed. This, in turn, is inserted into the hook for the embroidery process.
Design Library Catalogue: A programme that organises and catalogues collections of embroidery designs, allowing them to be searched by themes, stitches, size, and other features.
Tape: An old storage medium for designs in the form of punched tape. It has been almost entirely replaced by magnetic media, although the term is still in use.
Colorfill: A technique that combines embossing and embroidery, typically applied in this order, to create unique visual and textured effects.
Column: Stitches arranged very closely in a zigzag pattern, commonly used to create edges or text.
Compensation: Intentional adjustment of column widths or padding to counteract the stretching that embroidery may cause on the garment.
Italic: A text format with a rightward slant, used to stylise letters and add dynamism to the design.
D
Stitch Density: The number of stitches per unit area in an embroidery. Higher density results in denser and more detailed embroideries, while lower density leads to lighter and less compact embroideries.
Download: The process of transferring a file from the internet to your computer for subsequent use or storage.
Digitise: A modern term that replaces the concept of "punching". It refers to the process of designing an embroidery using specific software. This can be done by creating the design from scratch in the program, using an image as a template, or through the software's automatic functions to generate the embroidery.
Custom Design: Embroideries created from digitised sketches or by combining already digitised elements. These designs are unique and specific to each project or client.
Commercial Designs: Predefined embroidery designs available on disks, cards, or other media, created for general use. They are similar to clip-art libraries in graphic design and are not custom-made.
E
Edit: Manipulation of a design using a digitising program. It allows actions such as editing stitches or stitch blocks, scaling, repositioning elements, adding or removing parts of the design, and modifying machine commands to adjust the embroidery according to requirements.
Edit Stitches: A function in digitisation that allows you to move or remove individual stitches within a design to perfect it.
Emblem / Patch: A shield, insignia, or design that has been embroidered, woven, or printed. It is then trimmed and edged with a special stitch. It is applied to garments through sewing or adhesion and usually includes text or graphic elements.
Interfacing: Material placed on the back of the fabric to stabilise it during embroidery. It provides strength and reduces elasticity. There are different types based on thickness, composition, and method of removal (tear-away, cut-away, or soluble). In America, it is known as "pelón" due to the brand Pellon, and in Spain as "fliselina" due to the brand Vliese.
- Topping Interfacing: Interfacing placed on the front of pile fabrics, such as towels or velvet, to prevent interference with the embroidery. It is removed after the embroidery process either manually or using heat or water.
Scaling: The action of modifying the size of an embroidery design. It is generally limited to 10-20% to avoid stitch density issues, except in advanced software that automatically adjusts the density.
Scanner: A device that transfers physical images to the computer. It is used in embroidery to digitise paper designs and convert them into editable files in punching software.
Excess: Production of embroidery that exceeds the initially requested quantity. This may be due to errors or production adjustments.
F
TIFF or TIF File: Tagged Image File Format, widely used for storing high-quality images.
Felt: A non-woven material made from wool or hair, compacted through heat, moisture, and pressure. It is commonly used in the production of patches and embroidery samples due to its stability and durability.
- Short Stitch Filter: A feature in embroidery software that automatically removes stitches that are too short, as they do not add value to the design and may cause thread breakage during embroidery.
Flagging: Undesired movement of the fabric that follows the needle's motion, causing thread bunching and low-quality embroidery. This can be due to an improperly adjusted presser foot or inadequate tension of the fabric or stabiliser in the hoop.
Format: A specific data set or structure that a machine or program can interpret and use.
- Condensed or machine format: A specific embroidery file type for each brand of embroidery machine. It only allows basic adjustments such as rotating or scaling up to 10%, as it does not adapt the stitches to the size change. Embroidery software typically supports reading and saving in multiple formats.
- Expanded format: A simplified variant of the condensed format used for sending designs to embroidery machines. It allows the same limitations: rotating or scaling up to 10%, but without the possibility of making complex modifications to the design.
Puckering: An undesirable effect on the fabric caused by incorrect thread tension, a poorly placed hoop, or the use of unsuitable interfacings. It can also occur due to a blunt needle damaging the material.
Source: Complete digital alphabet designed for use on computers. Various types can be chosen depending on the style or design requirement.
- Sans-Serif Font Type: A font style that lacks strokes or serifs at the end of the letters. Example: Arial.
- Serif Font Type: A font style that includes strokes or serifs at the end of the main strokes of the letters. Example: Times New Roman.
G
Hook: A component that houses the bobbin case in the embroidery machine. It is essential in the formation of each stitch, making two complete rotations to ensure its point synchronises with the needle thread loop at the correct time and distance.
Jumbo Hook: A variant of the hook that accommodates bobbins with a larger thread capacity, reducing the need for frequent changes and enhancing efficiency in long embroidery projects.
Embossing: A technique that creates permanent reliefs on fabrics using moulds and heat pressing systems.
H
Hardware: The physical part of a computer or machine, such as internal components, printers, scanners, or modems, essential for the system's operation.
Thread: A fine cable made from natural or synthetic materials, such as rayon, cotton, polyester, metallics, or acrylics. It is used in embroidery and varies in sheen, strength, and texture depending on its composition.
- Special Threads: Threads designed to create specific effects in embroidery, such as increased shine, matte textures, or unique thicknesses.
K
Kern: The process of adjusting the space between characters in embroidered text to enhance its visual presentation.
L
Shuttle: See Schiffli.
Disk Reader: A unit, either internal or external, used to load punched designs stored on disks into the embroidery machine.
Machine Language: Specific codes and formats used by embroidery machine manufacturers for design interpretation.
Adhesive Letters: Letters or numbers cut from self-adhesive twill that are applied to garments, typically sportswear, and finished with a column stitch.
Lettering (Creating Text): The process of creating embroidered texts, either entirely with stitches or combined with appliqués.
Logo: Name, symbol, or trademark that identifies a company or organisation.
Canvas or Duck Cloth: A thick and durable fabric, commonly made from cotton, hemp, or linen, used in backpacks, tents, and other long-lasting products.
M
Machine of…: A machine that makes stitches using hook thread and needle. It includes both domestic sewing machines and computerised embroidery machines.
- Arm Machine: Multi-head machine driven by a single main shaft, where each head is connected to the shaft via gears, similar to industrial sewing machines.
- Cylindrical Arm Machine: A machine with a rounded arm that allows for embroidery on tubular fabrics around the cylinder, ideal for garments such as sleeves or trouser legs.
- Bridge Machine: A machine with heads suspended on a bridge that spans the entire machine, designed for embroidering pre-cut and metric textiles.
Marking: The action of making temporary marks on the fabric to centre the hoop and needle on the design.
Metafil: Needle with a longer eye, specifically designed for working with decorative or metallic threads.
Modular: A system in which multiple heads of an embroidery machine are independently controlled by a central computer.
Monogram: An embroidered design composed exclusively of letters, typically initials or names.
Motif: An individual element that is part of a complete embroidered design.
Tension Spring: A component that helps maintain the correct tension of the upper thread and detects possible thread breakages in embroidery machines.
Or
Offset: Function that allows the pantograph to be moved temporarily outside the work area and returned to its original position, commonly used for placing appliqués.
Origin: The starting point of an embroidery design on the machine.
P
Pantograph: A system of bars or shafts that supports and moves the frames in the X and Y directions, controlled mechanically or electronically to create the embroidery.
Pattern: Digitised embroidery design, ready to be used on an embroidery machine.
Backstitch / Backstitching: Straight stitches between two points, used to create details, edges, or support in a design.
Needle Plate: A metal plate positioned over the hook, featuring a central hole that allows the needle to pass through to form stitches.
SPC (Stitches per Centimetre): Unit of measurement for stitch density in embroidery.
SPM (Stitches per Minute): The speed at which an embroidery machine makes stitches, measured in stitches per minute.
Frame Press: A machine that facilitates the placement and even tensioning of fabric or garments in the frame.
Presser Foot: A metal piece that presses the fabric while the needle penetrates the material, ensuring it stays in place until the stitch is formed.
Pre-tensioner: Initial tension system that removes knots or loops in the thread and assists the main tensioner.
Stitch Processing: A function in embroidery software that allows the recalculation of stitches in extended format designs, adjusting sizes with density compensation.
Conversion Program: Software used to convert designs from one machine format to another.
Hooping: The process of placing the fabric or garment in the hoop, ensuring it is taut for embroidery.
Stitch: It is the basic unit of sewing that forms a design or pattern in embroidery. Each stitch is created when the needle passes through the fabric and the thread is tightened to hold it in place. There are different types of stitches (such as backstitch, satin stitch, or fill stitch) used depending on the effect or detail desired in the design.
- Lock Stitch or Knot: A series of three or four consecutive stitches to prevent the embroidery from unravelling after a thread cut or stitch jump.
- Chain Stitch: A stitch that forms a pattern similar to a chain, created with a single thread from beneath the fabric. It is performed using either manual or automatic machines.
- Triple stitch: A variant of the backstitch that goes over each stitch three times, providing greater thickness and durability.
- Chenille, Moss, or Loop Stitches: A type of stitch that creates loops in the thread, similar to the loops found in towels. Commonly used in sportswear and combined with appliqués, it requires specialised machines.
- Support or Reinforcement Stitches: Stitches placed beneath the final embroidery to stabilise the fabric and create raised effects. They are usually backstitches or low-density fills.
- Guide Stitches: Stitches used to centre the design or correctly position an applique.
- Satin stitches: Tight zigzag stitches, primarily used for edges and text.
Embroidery Stitch: Unit of measurement in embroidery, where 10 stitches are equivalent to 1 mm.
Cross Stitch: A type of embroidery that creates crosses with two intersecting stitches.
Punching: A technique that uses a punch tool instead of a needle to pierce the fabric and embroider outlines, leaving the holes as part of the final design.
R
Rescale: The action of changing the size of a design. It can cause density issues if the stitches do not adjust automatically.
Registration: A term originating from screen printing, referring to the precise alignment of colours within a design.
Filling: Large embroidery area covered with running stitches. Design parameters include stitch length, angle, and density.
- Complex Fill: A variation of filling that allows the creation of negative spaces or perforations in the design, using advanced punching software.
- Special Fill: Function in embroidery software to automatically apply patterns and textures to fill areas.
Repeat / Series: Reproduction of a design at regular intervals on a fabric.
Backstitching: A technique where the machine embroiders an entire area and then returns to the starting point with back-and-forth stitches.
S
Stitch jump: Movement of the hoop without forming stitches, used to advance in the design without embroidering.
Schiffli: An automatic embroidery technique originated in 1860 by Isaac Groebli, based on a shuttle that continuously feeds thread, named for its resemblance to a ship's hull.
Network System: A set of interconnected devices, such as printers and embroidery machines, that share data through wired or wireless connections.
Software: Programs used by computers to perform specific tasks, such as embroidery design.
Bonding: Permanent joining of fabrics using heat or adhesives.
T
Graphics tablet: A device formerly used for digitising, similar to a mouse, with integrated command menus. Its usage has declined with modern graphical environments.
Tension: The degree of tightness of the thread when forming stitches. It must be correctly adjusted in both the upper tension and the bobbin tension for uniform embroidery.
Tensioner: Device that regulates the thread tension during embroidery.
Snip Scissors: Small scissors specifically designed for cutting threads in the final stages of embroidery.
V
Verification: Testing process of a new embroidery design to identify and correct errors in the punching.
We hope this embroidery glossary has been helpful in better understanding the technical language of this fascinating technique. Whether you are a beginner or a professional, mastering these concepts will allow you to optimise your projects and make the most of the tools and resources available.
If you have any questions or think a term is missing, please leave us your comment! You can also contact our Customer Service department.
Remember that every day we post a plethora of ideas, offers, and updates on our social media about the different personalisation techniques. To ensure you don't miss anything, follow us on Instagram and TikTok. Oh, and don't forget to subscribe to our YouTube channel to continue learning with us.
See you in the next post!
WE WANT TO KNOW WHAT YOU THINK
You may also like